The History of Danemann Pianos
- by Macauley Sykes
- Oct 12, 2023
- 18 min read
Updated: Mar 1

W. Danemann & Company was established in 1893 by William (Wilhelm) Danemann, a German-born furniture designer and architect. Danemann grew to become one of Britain's best-known piano manufacturers with a strong reputation for excellent build quality. Danemann undoubtedly produced some of the UK's finest instruments at their factory in Islington, London and has been a brand close to the heart of Sykes & Sons for many years
William Danemann
William (Wilhelm) Danemann was born around the year 1864 in the quaint and picturesque town of Wittenburg, which is located approximately 60 kilometres north of Leipzig, Germany. Wittenburg is characterised by its traditional German architecture and local craftsmanship, which likely influenced Danemann's appreciation for design and artistry from a young age.
He emigrated to Britain sometime in the late 1800s and worked as a furniture designer in and around London.
The Beginning of Danemann Pianos
William Danemann's journey into the piano industry began when he was employed as a furniture designer to sketch a range of piano cabinets for a small piano manufacturer. This initial engagement allowed him to delve into the aesthetics and functionality of piano design, marrying form and function in a way that appealed to both musicians and homemakers alike.
When Danemann delivered his designs to the company, he was met with an unexpected twist of fate. To his dismay, he discovered that the firm had gone into receivership and was unable to pay him for his work. Despite this setback, Danemann's entrepreneurial spirit shone through and instead of simply cutting his losses and walking away from the situation, William saw a business opportunity and declared his intent to buy the failed company.
He approached the liquidators with a proposal that was both strategic and pragmatic, negotiating a price that took into account not only the assets of the company but also the amount owed to him for his design commission. This negotiation process was intricate, requiring Danemann to assess the value of the company's existing inventory and the potential for growth and survival in the competitive piano market. His business sense and determination ultimately led to a successful acquisition, marking the beginning of his journey into the world of piano manufacturing.
John Brinsmead
Some areas of the internet claim that William Danemann was a student of John Brinsmead (1814-1908), another notable piano manufacturer, but there is no evidence to support this claim. This assertion appears to be based on incomplete information and speculation, rather than concrete historical documentation.
John Brinsmead was a prominent figure in the British piano manufacturing landscape, celebrated for innovative designs and high-quality instruments. Brinsmead's work laid the foundation for many advancements in piano technology during that era. While it is certainly plausible that Danemann, as a contemporary of Brinsmead, could have been influenced by his work or even admired his craftsmanship, the claim of a direct student-teacher relationship lacks substantiation.
Trade Pianos
Danemann was originally set up as a manufacturer of "trade pianos", otherwise known as "Stencils". Trade pianos are produced by an often anonymous manufacturer (in this case Danemann) for retailers or distributors, who then have the instruments furnished at the later stages of production with a name of their choosing (often the store name or their private label).
Using trade pianos was (and is) particularly appealing to retailers, as it allows them to brand the instruments as their own, thereby enhancing their market presence and identity without the significant investment that is typically required for developing proprietary designs and operating production lines.
The design of trade pianos is typically generic, featuring a standardised aesthetic and structural framework that does not deviate significantly from model to model (hence the term "Stencil"). This uniformity is intentional, as using adaptable designs and similar components across different models significantly reduces production times and manufacturing costs.
Research & Development at Danemann
Danemann was among a large group of manufacturers producing trade pianos in London during this particular time. While producing trade pianos temporarily ensured a steady stream of revenue for the fledgling company, Danemann recognised that merely participating in this crowded market was not enough to secure the long-term success of the business. Danemann needed to distinguish itself from other manufacturers (many of whom were also producing similar instruments at comparable price points) if it had any hope of survival.
Danemann engaged in extensive research and development, dedicating significant resources and time to the exploration of various materials that would enhance the quality of sound and durability of their instruments while remaining competitively priced. This involved investigating traditional materials as well as innovative alternatives, assessing their acoustic properties and response to different environmental conditions. In addition to material selection, the company meticulously examined soundboard and bridge configurations, experimenting with different designs to optimise tonal quality and resonance.
Edgar, who was the son of William, made a significant impact on the family business when he joined the firm in the 1920s. Edgar had a deep interest in piano production and became the company's scale designer and quality manager. In this capacity, Edgar meticulously inspected every piano before it left the factory, employing a keen eye for detail and a profound understanding of piano construction.
His innovative approach to piano design led to the introduction of a remarkable feature known as the 'back bridge'. This unique component is particularly noteworthy as we don't believe it is found in any other British-made piano.
The back bridge functions as a counter bridge located on the back of the soundboard, effectively mirroring the pinned bridge situated at the front, over which the strings pass. The inclusion of the back bridge serves multiple purposes, significantly enhancing the tonal colour and consistency across all registers of the piano, while also contributing to the structural integrity of the soundboard, providing additional strength against the down-bearing pressure exerted by the strings.
Danemann not only sought to improve the overall performance of their instruments but also aimed to elevate their aesthetic appeal. This involved paying close attention to the visual aspects of their designs, such as finishes, inlays, and overall architecture of the cabinets.
Danemann earned a reputation for superior build quality, which set it apart from other manufacturers in the trade piano sector. The production of these stencil pianos remained the cornerstone of Danemann’s business model up until the 1940s.
Pohlmann & Son
In 1934, the long-established Pohlmann & Son of Halifax made the difficult decision to cease its piano production and subsequently closed its factory located in West Yorkshire.
Pohlmann was established in 1823 and, in its own right, was a notable piano manufacturer itself. Pohlmann controlled several valuable patents and is credited for being the first manufacturer in Britain to implement the overstrung bass in upright pianos.
In the wake of the closure, an agreement was reached between Danemann and Pohlmann.
Under the terms of this arrangement, a substantial portion of the manufacturing equipment that had been used at Pohlmann's premises was carefully transported to the Danemann Piano Works. This transition was not merely a logistical operation; it required meticulous planning to ensure that the equipment, which had been integral to the Pohlmann production process, could be effectively integrated into and improve Danemann's existing operations.
Once the equipment was in place, Danemann would continue to produce pianos under the esteemed Pohlmann name, ensuring that the quality and craftsmanship associated with the brand remained intact. Furthermore, as part of this agreement, Danemann would pay a relatively small royalty for each piano that bore the Pohlmann name, creating a guaranteed revenue stream for Pohlmann & Son while allowing them to maintain a presence in the piano market, albeit in a different capacity than before.
Henry Pohlmann's Scale Design
The agreement also stipulated that Danemann would gain the right to utilise the 'Pohlmann scale', another component of this agreement that was particularly advantageous for Danemann.
As a young man, Henry Pohlmann was sent to study piano design in the renowned Grotrian-Steinweg factory, located in the historic city of Braunschweig, Germany. This factory, famed for its meticulous craftsmanship, provided Henry with an invaluable education in the science of piano design. During his time there, he immersed himself in various aspects of piano construction, from the selection of high-quality materials to the precise engineering of the instrument's internal components.
After completing his studies and returning to Britain, Henry was eager to apply the extensive knowledge he had acquired during his time at the Grotrian Works. Drawing from his experiences, he set out to develop an excellent scale design that would enhance the tonal qualities and playability of his pianos.
The Pohlmann scale design was quickly incorporated into many of the instruments produced in Islington and would be further modified and improved upon by successive members of the Danemann family.
During the Second World War
At the outbreak of the war, the Ministry of Supply established comprehensive control over a wide array of materials that were critical to the war effort. These materials included, but were not limited to, wool, leather, and wood, but also a range of non-ferrous metals such as copper and zinc; all essential for piano production.
The Ministry's mandate was to ensure that these materials were allocated efficiently and effectively to manufacturers across various sectors, with a clear directive that first preference be given to war production. This meant that industries previously focused on consumer goods (such as pianos) were now redirected to meet the urgent demands of the military. This strategy by the Ministry of Supply was critical in ensuring that the armed forces were adequately equipped to face the challenges of warfare but meant that the materials which had once been sourced for the production of pianos suddenly found themselves redirected for military applications.
The rich woods for cabinets, the copper for their strings, the iron for the frames, and the fine leather and wool for action components were now essential for making uniforms, equipment, and other military necessities. Like many other manufacturers at the time, Danemann temporarily ceased the production of pianos during the Second World War and was wholly engaged in work for the British Government. Specifically, Danemann undertook projects for critical government departments, including the Admiralty, which was responsible for the Royal Navy.
This transition was not merely a matter of repurposing production lines; it also involved a comprehensive reallocation of skilled labour. The highly trained craftspeople, who had honed their skills in the delicate art of piano making, had to adapt quickly to new roles and responsibilities in support of the war effort, contributing their expertise to the fabrication of equipment that was vital to Britain's victory.
The Danemann Piano Works, once bustling with the sounds of piano assembly, was transformed into workshops where military components were produced, showcasing a remarkable versatility in the face of adversity and highlighting the collective effort of industries across Britain to prioritise the needs of the nation during a crisis.
After the Second World War
After the end of the Second World War, a significant transformation took place within the Danemann company, marking a pivotal shift in its operational focus and direction.

In this new era, Danemann decided to cease production of the trade pianos which had previously been a staple of their manufacturing output and redirect all of their resources and expertise towards the development of a completely new line of pianos that would be designed in-house and proudly carry the Danemann family name.
The development of this new line of models was approached with great care and attention to detail, reflecting a commitment to excellence that permeated every stage of the design and production process. These new models would be constructed from the very finest materials available to the trade, ensuring not only durability and longevity but also a premium feel that would resonate with discerning customers who sought a richer tonal quality, and a superior responsiveness of touch.
Danemann capitalised on their strong reputation which had already been established with the many retailers across the country who had been loyal customers and buyers of the previous trade pianos. Danemann was certainly able to leverage this established goodwill when introducing these new models to the market.
Prior to the war, the grand piano production at Danemann was characterised by a limited offering of small baby grands from their stencil enterprise. These pianos, although appealing to certain demographics, fell short of the expectations held by the more discerning musicians who Danemann was trying to attract. In response, Edgar Danemann undertook a significant redesign initiative. He envisioned a new baby grand piano that would replace the smaller trade piano that was previously produced by the firm.
This new model, measuring 5 feet 2 inches in length, was thoughtfully crafted to blend aesthetic appeal with enhanced acoustic capabilities. The new design aimed to provide a fuller sound and a more responsive touch, thereby catering to players who were in search of a versatile instrument that could perform well in a variety of musical settings.
After undergoing meticulous training which spanned several years, Peter Danemann, the son of the Edgar and grandson of William, also joined the family business. From a young age, Peter was immersed in the world of music and craftsmanship, and he inherited not only his father’s passion for piano building but also the deep-rooted values that the Danemann family had long upheld.
Through his extensive studies and hands-on experience, Peter cultivated an intricate and nuanced understanding of piano construction. This included a profound grasp of scale design, which is essential for determining the tonal quality and range of the instrument, as well as a detailed knowledge of action and keyboard geometry, which plays a vital role in the responsiveness and playability of the piano. His enthusiasm for the instrument was palpable, driving him to explore innovative techniques and materials that could enhance the sound and performance of the pianos produced by the Danemann factory.
As he collaborated closely with his father, Peter utilised his burgeoning skill set and comprehensive understanding of piano mechanics to contribute to the development of the new Danemann models. Peter was particularly focused on improving upon the inherited Pohlmann scale and was able to identify areas for enhancement and implement changes that would result in a richer tonal palette and greater dynamic range.
Peter first designed two modern upright pianos named the PJ and the PJA, which were meticulously crafted to reflect both aesthetic beauty and superior sound quality. These two innovative models would become the foundation for all of Danemann's domestic piano offerings.
Both models were characterised by their elegant design and robust construction and were an immediate commercial success.
Following the triumph of the upright models, Peter then turned his attention to the grand piano segment, designing two new models that would further enhance Danemann's reputation in the world of musical instruments. The PJB, a boudoir grand, was crafted with an emphasis on intimacy and warmth, making it an ideal choice for smaller spaces and personal performances. It offered a delightful balance of size and sound, allowing musicians to enjoy a rich tonal experience without the overwhelming presence of larger models. On the other hand, the PJC was a concert grand, designed to meet the rigorous demands of professional performance settings. This model boasted a larger soundboard and enhanced resonance capabilities, enabling it to project a powerful sound that could fill concert halls and work as part of an orchestra.
These Danemann pianos quickly garnered acclaim from musicians and music educators alike, who were immediately drawn to their sweet, rich, and full-bodied tone. The tonal quality of these instruments was remarkably similar to that of pianos originating from Germany, which were often regarded as the gold standard in the industry.
Becoming a Household Name
Danemann earned several lucrative contracts with some of the most recognised names in the British retail, leisure, and entertainment sectors, which marked a significant turning point in the company’s trajectory. These contracts were not merely financial agreements; they represented a strategic partnership with industry leaders, allowing Danemann to showcase its products and services to a wider audience. The collaboration with well-established brands provided Danemann with invaluable exposure, enabling the company to leverage the reputation and customer base of its partners. This was the beginning of Danemann's transition from being a manufacturer which only the trade knew of, to a household name.
Danemann pianos, in particular, formed the stock of the musical instrument department at Harrods of Knightsbridge, a prestigious establishment renowned for offering luxury goods to an elite clientele. Within the opulent surroundings of Harrods, Danemann pianos were showcased as symbols of excellence and sophistication, attracting the attention of both amateur musicians and professional performers alike.
Moreover, Danemann pianos were utilised on the vessels operated by P&O Cruises, where they provided the perfect accompaniment to the luxurious experience offered to passengers. These pianos contributed to the onboard entertainment, enhancing the ambience of dining rooms and lounges, and allowing guests to enjoy live music while sailing through stunning seascapes. The presence of Danemann instruments on such prestigious cruise liners highlighted the brand's commitment to quality and its ability to meet the high standards expected in the leisure industry.
In addition to their presence in retail and leisure, Danemann pianos were found throughout eminent venues all across the UK, including the renowned Royal Festival Hall, a landmark venue celebrated for its exceptional acoustics and hosting a wide array of performances. The choice of Danemann pianos in such a distinguished location further solidified the brand's reputation as a preferred choice among concert halls and performance spaces, where sound quality and aesthetic appeal are paramount.
Furthermore, Danemann also supplied instruments to British embassies across the globe, showcasing the brand's international reach and influence. Each piano was meticulously crafted with individual modifications tailored to suit the particular climates of the locations to which they were being exported. This attention to detail ensured that the instruments would perform optimally, regardless of the environmental conditions they faced.
Danemann School Pianos

Danemann's capability and willingness to build pianos to extremely rigid specifications established them as a leading manufacturer of choice for numerous educational authorities throughout the United Kingdom.
Danemann was entrusted to supply pianos to many of the country's most prestigious institutions, such as the Royal College of Music and the Royal Northern College of Music.
These institutions are renowned for their rigorous training programs which nurture the talents of the next generations of musicians. Remarkably, many of the instruments supplied by Danemann during the 1960s until the 1980s are still actively serviced and in use within these institutions today.
These robust instruments, designed to withstand the rigours of daily use in a busy educational school environment, are instantly recognisable and are what Danemann is best remembered for by most people, particularly if their school had one. For a significant period, these school pianos represented a remarkable 80% of Danemann's overall production output. This substantial percentage underscores the vital role that educational institutions eventually played in the company's business model and financial stability.
However, while these educational pianos are certainly a testament to Danemann's commitment to creating long-lasting pianos, these instruments don't represent the best of Danemann's production.
The London County Council made several stipulations on the construction of educational pianos and Danemann needed to strictly adhere to the various stipulations and guidelines established by the educational authorities if the firm were to maintain its strong relationships and continue supplying schools and colleges across the country.
The case components of these pianos were mandated to be made from solid oak, for its strength and resistance to wear, with little thought to the fact that the dense nature of oak makes it particularly good at blocking, reflecting, and absorbing soundwaves which is not conducive to the tonal qualities of a piano.
The manufacturers of these school pianos were forced to try and circumvent the issue introduced by the oak cabinets by using very hard felt on their hammers. This resulted in pianos which had lots of volume but often lacked warmth in the tone. They instead had quite a strident tone that is remembered as being almost overbearing and harsh on the ears.
Additionally, the use of zinc-plated music wire was mandated, over polished music wire, because of its corrosion-inhibitive properties. While zinc-plated music wire offers some protective benefits in damp conditions, it is tonally inferior to the polished music wire that was used in Danemann's domestic pianos. The polished music wire is known for its superior tonal quality, producing a clearer and more resonant sound that is highly valued in personal and professional settings. In addition to its tonal limitations, zinc-plated music wire tends to become brittle as it ages. This brittleness is so pronounced that it has earned a colloquial nickname in the trade: "chicken wire."
Overall, the materials and construction methods chosen for school models reflect a balance between practicality, cost-effectiveness, and the specific needs of educational institutions, while also highlighting the inherent trade-offs in with different types of materials used in piano manufacturing.
Thankfully, Danemann had complete autonomy over their domestic models and the differences show. Their domestic pianos are favoured for their sweet, warm, and full-bodied tone, more appropriate for the intimate audience of the family home, rather than a school hall.
Factory closure
Unable to effectively compete with the comparatively low retail prices of pianos imported from abroad, as well as facing the significant challenges posed by the diminishing school budgets of the 1970s and 80s, Danemann found itself struggling to stay in business.
The influx of cheaper foreign-made pianos made it increasingly difficult for Danemann to maintain its market share and profitability. This situation was exacerbated by the financial constraints faced by educational institutions during this period, as schools were forced to cut back on arts programs, including music education, due to tight budgets. Consequently, the demand for quality pianos, which had historically been a staple in schools and music programs, began to decline sharply.
As a result of these compounding pressures, Danemann struggled to remain afloat in a rapidly changing economic landscape. The once-thriving company, known for its craftsmanship and quality, found itself at a crossroads, grappling with the realities of a competitive market that favoured lower-priced alternatives.
In a bid to secure the future of the business and ensure its survival amidst these challenges, Tom Danemann made the difficult decision to sell both the business and the premises to John Broadwood and Sons Ltd in 1982. Broadwood had planned to use the Danemann Piano Works and the existing workforce to construct at least six models of Broadwood while concurrently manufacturing eight models of Danemann pianos, thus maintaining the brand's identity and legacy.
However, this well-laid plan was significantly undermined by the financial difficulties that Broadwood unfortunately inherited upon taking control of Danemann. These financial woes were not merely a minor setback; they were substantial enough to threaten the viability of the entire operation.
To stabilise the situation and fund the ambitious production plans, the new parent company decided to secure a loan amounting to £250,000 from the Islington Borough Council.
This loan was seen as a crucial lifeline, intended to provide the necessary capital to meet operational costs and fulfil the production goals set for both the Broadwood and Danemann models. Sadly, the financial landscape proved to be more challenging than anticipated, and the company found itself unable to meet the repayment obligations associated with the loan. As the financial strain continued to escalate, the situation reached a critical point in 1984 when the Islington Borough Council called in the receivers.
The receivership process initiated a thorough review of the company's assets and liabilities, ultimately leading to the formal closure of the Danemann Piano Company in 1985 during the subsequent insolvency proceedings. This closure not only signified the end of an era for a respected brand but also highlighted the broader challenges faced by traditional manufacturers in an increasingly competitive and financially volatile market.
The rights to the Danemann name and much of the equipment were sold to a Welsh firm which took production of Danemann Pianos to Wales and continued to make the instruments up until 1994.
The Danemann Piano Works

After the closure of the Danemann Piano Company, the factory which had housed the family enterprise for the last 90 years was converted into a multi-use premises and renamed The Ivories. The Ivories is still in use today and is comprised of a range of modern open plan studios and offices over a ground and two upper floors.
The building's former life has been commemorated with a pair of iron gates in the shape of two interlocking grand pianos which are erected at the former goods entrance.
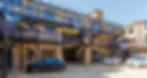
Each space has its own entrance onto a central shared courtyard, with those on the upperfloors linked via elegantly fabricated steel walkways with a sweeping staircase in the centre.
Despite at least two renovations, the building has retained many of its original features, such as the art deco gable, skylights, and decorative brickwork.
The premises contains several businesses, including a retail and workshop space for flutes, several gyms, a therapy centre for children, and an artisan bakery, to name a few.
Present Day
In 2015, the rights to the Danemann name were sold once again.
This time, by a firm that had a clear intention of leveraging the famous name to market a new line of instruments that are manufactured in China.
The import of these newly branded pianos commenced in 2017, marking a significant shift in the legacy of the Danemann brand. While this latest generation of Danemann pianos proudly displays the same logo that is emblematic of their British predecessors, it is important to note that they bear little resemblance to the original instruments that were crafted in Britain with painstaking attention.
Instead, these modern iterations contain no designs or engineering principles from the original company or the skilled craftspeople who were instrumental in building the Daneman reputation over the decades.
Once regarded as one of Britain's most well-respected piano makers, Danemann is sadly a mere name that adorns what can be likened to the modern-day equivalent of a trade piano.
This transformation highlights a broader trend in the music industry, where heritage brands are often repurposed for mass production, leading to a dilution of their historical significance and craftsmanship. The original Danemann pianos were known for their exquisite sound quality, robust construction, and the unique character that each instrument possessed. In contrast, the current offerings may lack the soul and individuality that were once hallmarks of the brand.
As a result, enthusiasts and musicians who once revered the Danemann name for its legacy of excellence may find themselves disheartened by the current state of the brand, which now prioritizes production efficiency over the artistry and tradition that defined its past.
Danemann pianos at Sykes & Sons

Danemann is a brand that holds a significant and cherished place in the heart of Sykes & Sons, embodying a rich history and deep connection that transcends just business transactions.
This relationship goes beyond the ordinary, as it is intertwined with personal experiences and professional milestones that have shaped the professional identity of our company owner.
To understand the profound significance of Danemann to Sykes & Sons, one must look back to the very beginning of Macauley’s journey in the world of pianos. The first piano that Macauley ever owned was a Danemann, and his journey in the piano trade began with stripping and refinishing ex-school Danemanns, which formed our fleet of hire pianos.
Furthermore, the first grand piano that Macauley restored and subsequently sold was also a Danemann, marking a significant milestone in his professional journey and further solidifying his connection to the brand.

At Sykes & Sons, we take great pride in the fact that we exclusively stock British-made Danemann pianos, each one having undergone a thorough and meticulous reconditioning process in our workshop. This process is carried out with a deep respect for the original makers, ensuring that the integrity and character of each instrument is preserved.
Our commitment to quality is unwavering; we believe that the craftsmanship inherent in British-made Danemann pianos is unparalleled, which is why we consistently strive to maintain a diverse selection of these exceptional instruments in our inventory. Our dedication to this brand is not merely about business; it is about honouring a legacy and celebrating the artistry that goes into each piano.
As Danemann is one of our specialities, we have a considerable in-depth understanding of the brand. Our extensive experience with Danemann pianos equips us with the knowledge necessary to identify key aspects that contribute to their quality and performance. We know exactly what to look for when evaluating these instruments, ensuring that we are only offering the best possible quality of Danemann pianos to our customers.
This expertise allows us to confidently recommend the right piano for each individual, knowing that we are providing not just a product, but a piece of musical heritage that will be cherished for years to come.