The Knight K15
- by Macauley Sykes
- Feb 27, 2024
- 8 min read
Updated: Mar 1
Unlike most UK-based manufacturers, who typically focused on domestic sales and local markets, Alfred Knight recognised the immense potential of the expansive American piano market and made a strategic decision to craft a line of pianos to meet the tastes and preferences of American pianists.
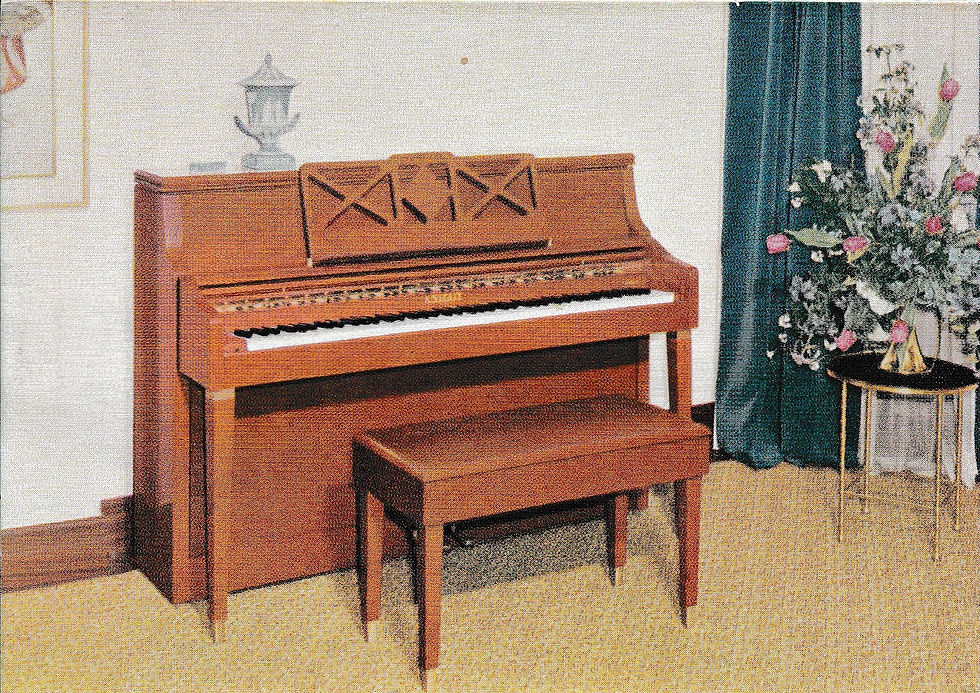
Knight introduced several models that were specifically for export across the Atlantic. The K20 (photographed) was based on the existing K6, and the K30 was based on the famous K10. The K20 and K30 models were essentially the same pianos as the previous K6 and K10, but were now clad in carefully crafted spinet-style cases, an aesthetic that had gained significant popularity in the United States during the 1950s.
By basing the K20 and the K30 on tried and tested models, Knight ensured that the same exceptional levels of sound and performance—which had long been hallmarks of the firm—would be effortlessly carried forward in these new iterations.
However, Alfred desired to expand his company's offerings to American musicians even further by developing a third piano model. This model was envisioned as an even smaller and more compact spinet-style piano that would appeal to a wider audience on the American continent, where space constraints in urban living were becoming increasingly prevalent.
Knight faced a significant challenge in this endeavour. At the time, no existing models within the company's current lineup could simply be reclad in a new cabinet and be of the desired height.
This lack of a suitable base model meant that Knight could not entirely rely on any pre-existing frameworks and would have to take a comprehensive approach to design and create an entirely new model from the ground up. This would require not only innovative design work but also careful consideration of the materials, construction techniques, and acoustic properties that would ensure the new spinet-style piano met the high standards expected by customers.
To create this new model, Knight needed to explore various configurations and mechanisms that would allow for a reduced height without sacrificing sound quality or playability. This process involved extensive prototyping and testing to ensure that the instrument would produce a rich and full sound while being comfortable to play, despite its compact size. The challenge was not merely about aesthetic appeal; it was about engineering an instrument that could proudly stand alongside its larger counterparts.
Frame and Soundboard
Spinet pianos, especially those of such a short height, usually have short strings and small soundboards, neither of which are conducive to volume or good tonal characteristics.

To overcome the challenge of string length, Knight drew upon his extensive experience and expertise, particularly referencing his designs for the frames he previously developed for the pianos in his renowned "K Range".
The engineering behind these frames aimed to achieve the longest possible string length while providing exceptional strength and stability for the instrument.
These frames utilised a full-perimeter design and were built on the girder principle from heavy-duty cast iron. These frames reportedly have twice the strength of frames fitted to the average piano and this extra strength of the frame allowed Knight to dispense the brace bar normally found in the treble section of upright pianos. A brace bar requires a notch (a gap) in the long bridge to pass through and this notch can cause tonal discrepancies in the notes on either side.

Knight was able to create a new frame, of the desired height, which also retained all of the features and principles included in his other renowned models. This innovative frame not only met the specific height requirements but also incorporated the essential design elements that made Knight's previous models so successful and widely appreciated in the industry.
The string angle, which enabled the additional length, also allowed Knight to reposition the bass bridge to a more optimal location, further away from the edge of the soundboard, to enhance amplification.
Knight used a double-carved main-bridge which was laminated and capped with quarter sawn beech. This construction method eliminates dissipation of the vibrations, which take the line of least resistance, and follow the laminations.
For this new model to rival the sound and tonal qualities of much larger instruments, Knight needed to incorporate the largest possible soundboard in this piano, despite its restrictive dimensions. Knight secured the soundboard onto a four-post quarter-sawn hardwood back with the frame anchored on top, sandwiching the soundboard between. This exceptionally sturdy construction method ensured the piano would be as strong as possible.

Knight carefully selected forest-grown spruce from the Northern slopes of European mountain ranges for the soundboards in the K range pianos. The long, regular and uninterrupted growing conditions on the Southern Carpathians result in trees with large interiors which are comprised of very straight grains, minimal knots, and very consistent growth rings, making the wood the desired density, strength, and elasticity required for the all-important soundboard.
The spruce was air-seasoned and kiln-dried at the Knight factory, and the completed soundboards were finished in a specially developed moisture-resistant varnish which not only protected the natural material but also enhanced its tonal qualities.
Knight's Drop-Action
In a typical upright piano, as well as in all of those within the existing 'K Range', the bottom of the action is positioned above the height of the keyboard. However, for this new model to achieve the desired finished height, the base of the action would need to be situated lower than the keyboard itself. This particular arrangement is commonly found in spinet pianos and usually necessitates very short keys which are tied to what is typically a very compressed action with an often complicated system of levers and linkages.
This can have a detrimental impact on how the piano feels to the player and has contributed to the reputation of spinet pianos being somewhat uncomfortable to play and very unresponsive in poorly designed or maintained examples. These extra moving parts can also make servicing and maintaining the piano a daunting task for the technician.

Knight attached great importance to the performance and serviceability of this instrument.
To achieve a satisfactory result, Knight understood that he needed to incorporate an action geometry which was identical to that found in his larger instruments. This involved not only theoretical calculations but also practical testing, as he sought to create an instrument that would respond accurately to the subtleties of a pianist's technique and break away from the drawbacks that are commonly associated with spinets.
Knight was able to include a full-sized action in the K15 by carefully determining where it needed to sit within the piano and then designing a system which accommodated this without introducing a heavily complicated array of mechanics which were prone to failure.
Knight designed an 'undercarriage', which was permanently affixed inside of the piano. The undercarriage is comprised of minimal moving parts and was secured through special fixing points on the piano's frame and sturdy key-bed.
The keys were carefully designed with special attention paid to the 'balance point' to ensure that the keys offered the precise amount of leverage over the action while maintaining the optimal amount of key travel and control.
By carefully examining the intricate mechanics and interactions between the various components of the keys and action, Knight was able to ensure that the touch and response was indistinguishable from that of a larger piano and would meet the high standards expected by his customers.
What is especially helpful for the technician is the fact that the action can be lifted out of the piano during maintenance without unhooking it from each key, which removes much of the dreaded work from servicing a spinet.
The Casework
Alfred ensured the most stable cabinets by fabricating the case components from very heavy, cross-grained laminated wood which was meticulously engineered to resist warping and bending, even in the most extreme environmental conditions. The cross-graining technique, which involves layering thin sheets of wood in alternating grain directions, effectively counteracts the natural tendencies of wood to expand and contract with changes in humidity and temperature. This thoughtful engineering ensured that the cabinets remained stable, whether they went to the tropical climate of southernmost Florida, the rain-drenched mountains of the northwest coast, or the drought-ridden deserts of the southwestern United States.
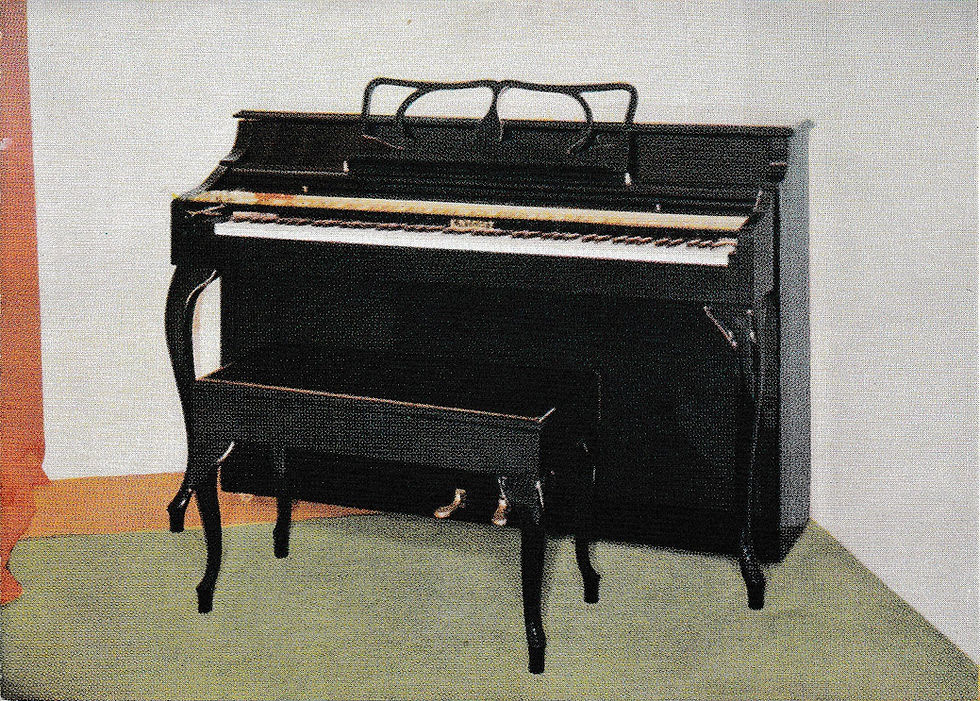
The K15 was made available in an extensive and diverse variety of different finishes, showcasing a remarkable range that catered to the tastes of various customers. These finishes included everything from luxurious and exotic veneers, to the contemporary option of black polyester that exuded a modern aesthetic. Each finish was carefully crafted to enhance the natural beauty of the wood or the sleekness of synthetic material, ensuring that every K15 served as a stunning visual centerpiece in any room.
To secure this impressive selection of veneers, representatives of The Knight Piano Company travelled the world, from France, Burma, Africa, and South and Central America, to hand-select the woods that would eventually be used to produce their pianos. Their mission was to use the finest materials available, meticulously choosing woods that would ultimately contribute to the unique character and quality of their pianos.
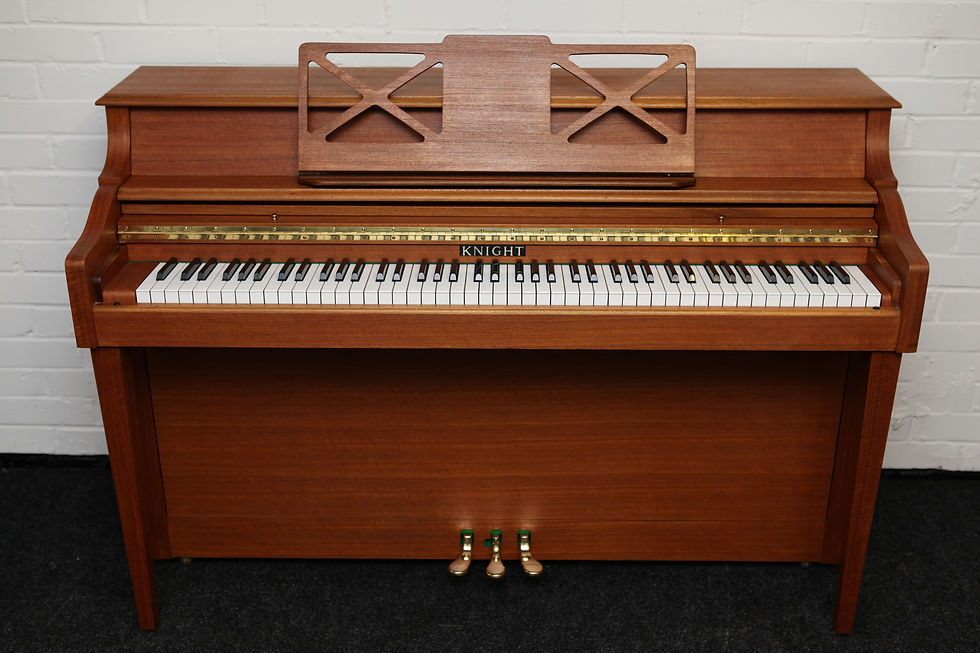
Customers could choose from a vast palette of various species of wood, from mahogany, known for its warm tones and fine grain; Brazilian walnut, celebrated for its durability and rich, dark hues; French walnut, which offers a unique blend of light and dark shades; Burmese teak, prized for its water resistance and natural oils; Brazilian rosewood, famous for its striking patterns and deep color variations; and many more exquisite options.
Knight also went to extreme lengths to assiduously train a dedicated team of highly skilled craftspeople in the intricate and specialised art of veneer cutting, matching, and grafting. This training process was not merely a brief introduction; it involved a comprehensive curriculum which covered the nuances of wood types, the intricacies of grain patterns, and the various techniques required to achieve precision in every cut.
Understanding that the quality of the final product depended heavily on the craftsmanship involved, Knight meticulously selected each team member for their attention to detail and passion for woodworking. In addition to the rigorous training program, Knight invested significantly in acquiring the most preeminent and advanced equipment available in the industry. This included sophisticated infrared curing systems, state-of-the-art veneer saws, and precision cutting tools, that allowed the craftspeople to create seamless joins in perfectly aligned grain patterns.
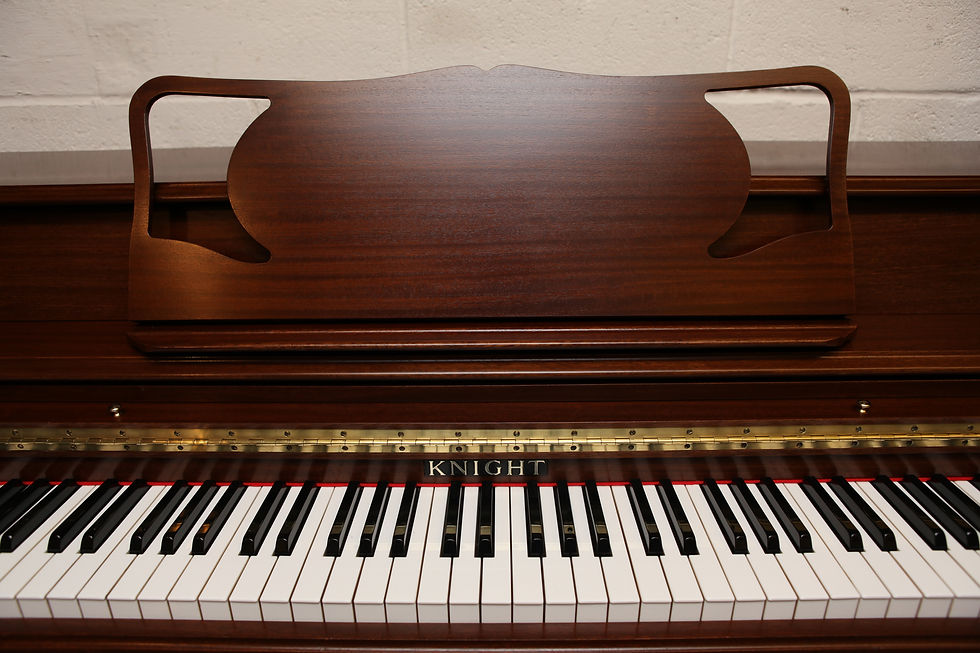
By equipping the team with such high-quality tools to work with such fine materials, Knight ensured that they could achieve the most flawless final finish possible, elevating their work to an art form. Each piece produced by the team reflected not only their skill and dedication but also Knight's commitment to excellence in craftsmanship, resulting in stunning pianos that stood out in the marketplace.
In addition to different veneers and finishes, Knight also offered customers a choice in different leg types, from square and round tapered to Queen Anne style, and a variety of music desk types. This wide selection not only catered to the personal tastes and interior design preferences but also allows for a high degree of customisation, ensuring that each cabinet can perfectly complement its surroundings.
The K15 was not only popular over the pond, it was a commercial success here in the UK too. It is widely regarded as one of Alfred's most notable triumphs in piano engineering and design. Each K15 piano is a testament to Knight's innovative spirit, featuring advanced elements that successfully pushed the boundaries of piano design.
Alfred Knight dedicated his life to producing pianos of exceptional quality, and through his unwavering commitment to craftsmanship, he is considered to be one of the finest piano designers that England has ever had to offer. Throughout his illustrious career, he designed some of the most well-regarded pianos in British history, each one embodying his passion for excellence and his relentless pursuit of perfection.
Knight Pianos at Sykes & Sons
As Knight is one of our specialities, we have a considerable in-depth understanding of the brand. Our extensive experience with Knight pianos equips us with the knowledge necessary to identify key aspects that contribute to their quality and performance. We know exactly what to look for when evaluating these instruments, ensuring that we are only offering the best possible quality of Knight pianos to our customers.
This expertise allows us to confidently recommend the right piano for each individual, knowing that we are providing not just a product, but a piece of musical heritage that will be cherished for years to come.
Komentarai